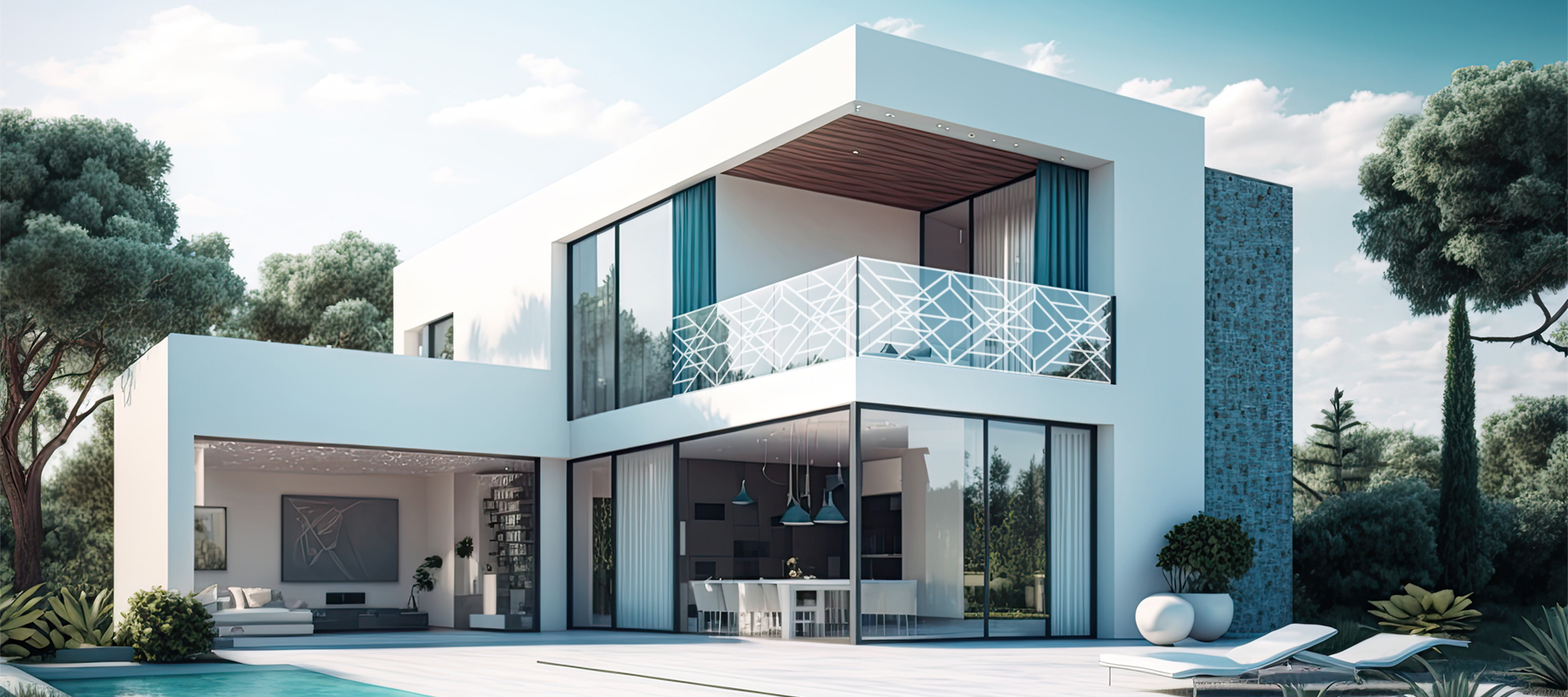
Keramischer Digitaldruck auf Glasgeländer bietet ganz neue Möglichkeiten der Gebäudegestaltung.
Der keramische Digitaldruck hat bereits in vielen Bereichen Einzug gehalten. So bietet die Firma Fritsche beispielsweise schon seit langem bedruckte Küchenrückwände an, aber auch Raumteiler und Glastüren lassen sich auf diese Weise verschönern. Ein neues Kapitel im Bereich Glasdruck sind bedruckte Glasgeländer. Ob im Innen- oder Außenbereich ist hierbei egal, denn der keramische Digitaldruck ist absolut witterungsbeständig.
Sämtliche Motive können schlicht in Weiß oder auch in Farbe gedruckt werden. Auch das Glas selbst darf färbig sein, so können Sie Ihr gewünschtes Muster z.B. auch auf modernem Grauglas drucken lassen.
Glasdruckbestellung völlig unkompliziert:
In unserem Katalog finden Sie viele vorgefertigte Motive – das erleichtert die Auswahl und macht die gesamte Abwicklung einfach und schnell. Begeistern Sie Ihre Kunden mit dieser neuen Gestaltungsmöglichkeit! Der Druck kann auch zur Folie hin gefertigt werden, so dass beide Oberflächen glatt und leicht zu reinigen sind.
DOWNLOADS
Sie sehen gerade einen Platzhalterinhalt von yumpu. Um auf den eigentlichen Inhalt zuzugreifen, klicken Sie auf den Button unten. Bitte beachten Sie, dass dabei Daten an Drittanbieter weitergegeben werden.
‚